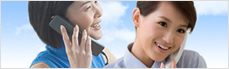
電話:86-0511-86389378
傳真:86-0511-86382256
聯系人:嚴國峰
手機:13914586636
網址 :http://www.kbxgaj.com
大型鎂合金壓鑄件的沖鉚連接技術及應用
鎂合金的密度 1.8g/cm3,大致為鋁合金密度的 1/3,是實際工程應用中最輕的金屬結構材料。通過在乘用車中批量應用鎂合金鑄件可以有效地降低整車重量,提高燃油經濟性。根據目前的通用計算方法乘用車總質量每減輕 100kg,燃油耗可降低 5%。如果每輛汽車使用 70kg 鎂合金部件,CO2年排放量能減少 30%以上。與目前汽車輕量化材料相互替代過程中,鋁合金和工程塑料獲得廣泛應用相比,鎂合金部件明顯落后。在目前汽車零部件一級供應商中,只有極少數公司供應鎂合金產品。鎂合金部件的全過程總成本的比較,包括材料、制造、防腐、連接裝配、維修等方面的原因是制約其廣泛應用的重要因素,其中如何保障鎂合金部件與其它部件可靠地連接是其中一個重要的障礙。
應用鎂合金部件的驅動力及發展趨勢
隨著節能環保要求的逐步嚴格,從 A 級車到 C 級車都面臨著減低整車重量,減小排放以滿足環保要求。根據歐盟法規,在 2020 年乘用車的 CO2排放將從 2015 年的 130g/km 下降至 95g/km,這就意味著燃油消耗必須從目前的水平下降 25%才能夠滿足需求。提高發動機的燃燒效率,減小整車重量,減小空氣阻力,減小滾動阻力和減小摩擦等方法均被用來降低燃油消耗。在上述方法中,降低整車重量大致可以降低燃油消耗 9%。為了最大限度地降低整車重量,大型集成結構的鎂合金部件的應用就成為汽車輕量化工作中的一個重要的研究與開發方向。
目前,鎂合金車門內板、儀表板、前端水箱框架等大型鎂合金鑄件已經在乘用車上獲得了廣泛的應用。此類部件的共同特點是尺寸較大,通常長度大于 1m,并充分利用鑄造過程的優勢,最大限度地集成了周邊的部件,形成了結構復雜的大型集成鑄件。這些大型集成鑄件通常需要采用 3000t 以上的壓鑄機才能夠滿足生產。
車身連接技術
隨著輕量化車身開發的迫切,越來越多的連接方式被開發出來。總體上來說,車身的連接技術可以分為熱連接和冷連接兩種方式。熱連接主要包括 MIG 焊、電阻焊和激光焊等方法,冷連接主要包括粘接、自攻螺釘和自沖鉚接等方法。目前大型鎂合金鑄件的主要生產工藝是高壓鑄造,鑄件內部不可避免的含有少量氣體,加之考慮到鎂合金易于氧化的特性及較低的電極電位,采用焊接方式進行連接難以實現。冷連接成為鎂合金部件主要的連接方式,如何合理的選擇連接方式以獲得良好的連接強度并避免連接電偶腐蝕問題就成為目前開發的重點。
鎂合金中通道鑄件連接技術開發
鑄件需要通過螺紋和螺柱兩種連接方式與周圍的部件進行連接。按照一般部件的連接方式考慮,螺紋連接可以通過在鑄件上加工螺紋孔的方式形成連接;通過在鑄件上焊接螺柱的方式形成螺柱連接。然而,對大型鎂合金鑄件進行螺紋加工,不僅容易出現加工廢品,而且會顯著增加生產成本,導致客戶無法接受鑄件的價格。由于鎂合金鑄件的可焊性較差,焊接螺柱幾乎沒有可能實現。
通過在鑄件上預設孔,并應用帶有螺紋的彈簧夾片的方式解決了螺紋連接問題。如何實現螺柱的連接則是一個比較困難的問題,先后考慮了多種技術方案。焊接:考慮到可焊性的問題,焊接方案被放棄;結構膠:考慮采用結構膠粘接方案可能會出現疲勞和底紋脆性問題,沒有采用此方案。鑲鑄:在鎂合金方向盤骨架的生產中曾經廣泛采用過鑲鑄工藝,但是直接鑲鑄螺柱的成功概率和強度都不高,而且模具比較復雜,下鑲件時會顯著影響生產效率。預鑄安裝孔:安裝孔公差不易控制,可能還需要機械加工。自沖鉚連接:預鑄孔尺寸要求不高,可應用涂層防止電偶腐蝕,可以較好地滿足螺柱的連接強度和尺寸精度要求,最終選擇此方法完成了螺柱的連接設計,實現了鑄件的批量生產。
本文摘自《中國有色金屬報》。
鋁壓鑄件加工廠家推薦閱讀: